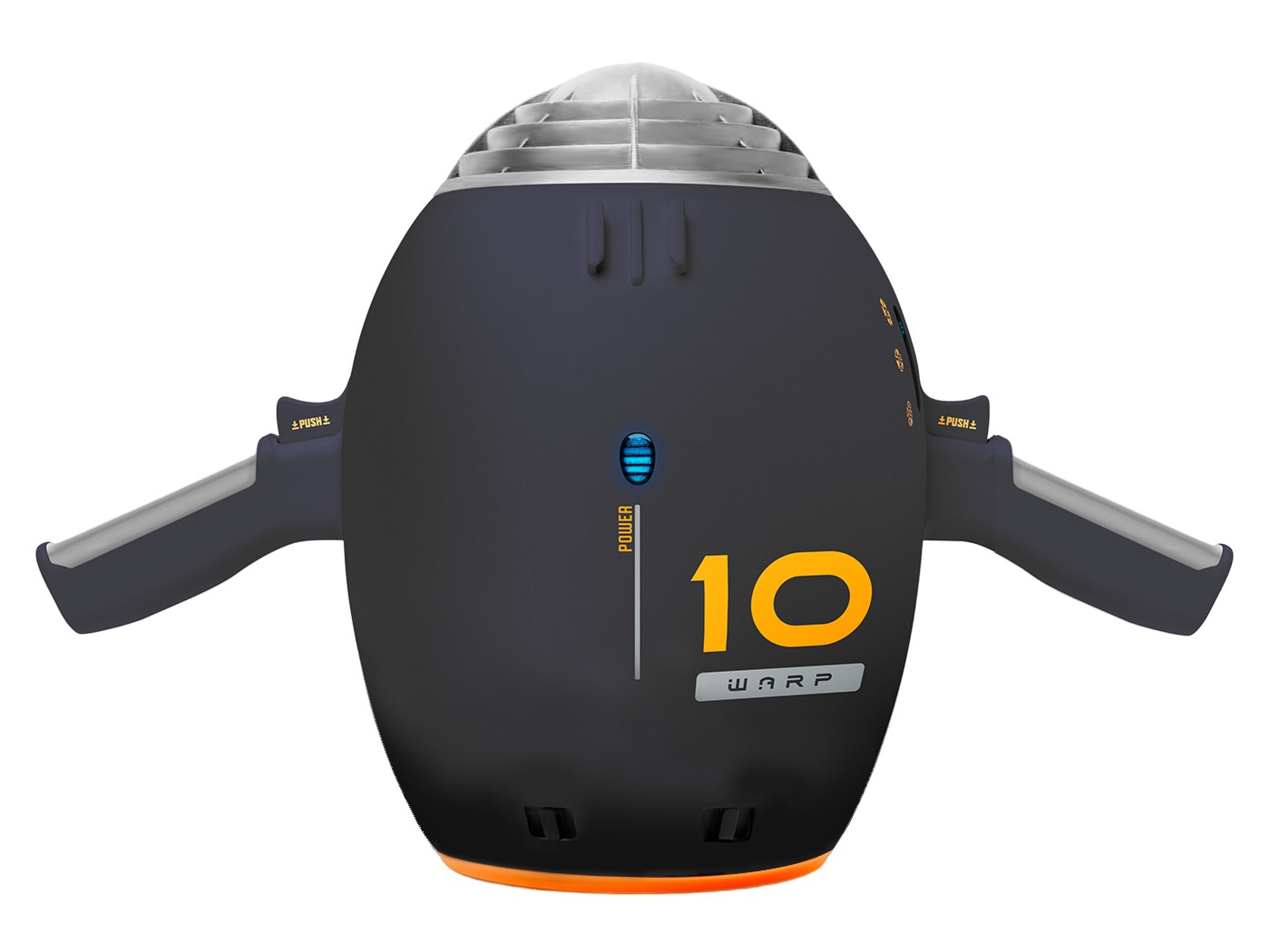
Underwater Scooter for Diving
Underwater Scooter for Diving
New Brushless DC Motor High Torque Rated Torque 30 Nm CAN BUS
The Stealth Pan Tilt Minibot features a GoPro camera for a stable live video feed.
3D LiDAR 256 Lines Point Cloud Benewake AD2-S-X3 Long Range 350m for ADAS Autonomous Driving Truck – More Details
A fully Arduino IDE-compatible microcontroller.
Light Duty Mini Tracked UGV Robot Chassis with RC Control
Raspberry Pi Case with Touchscreen
Leading Companies and Institutions Buy from Oz Robotics
World’s Leading Schools Buy from Oz Robotics
Bluetooth Low Energy Module